Low Pressure Die Casting
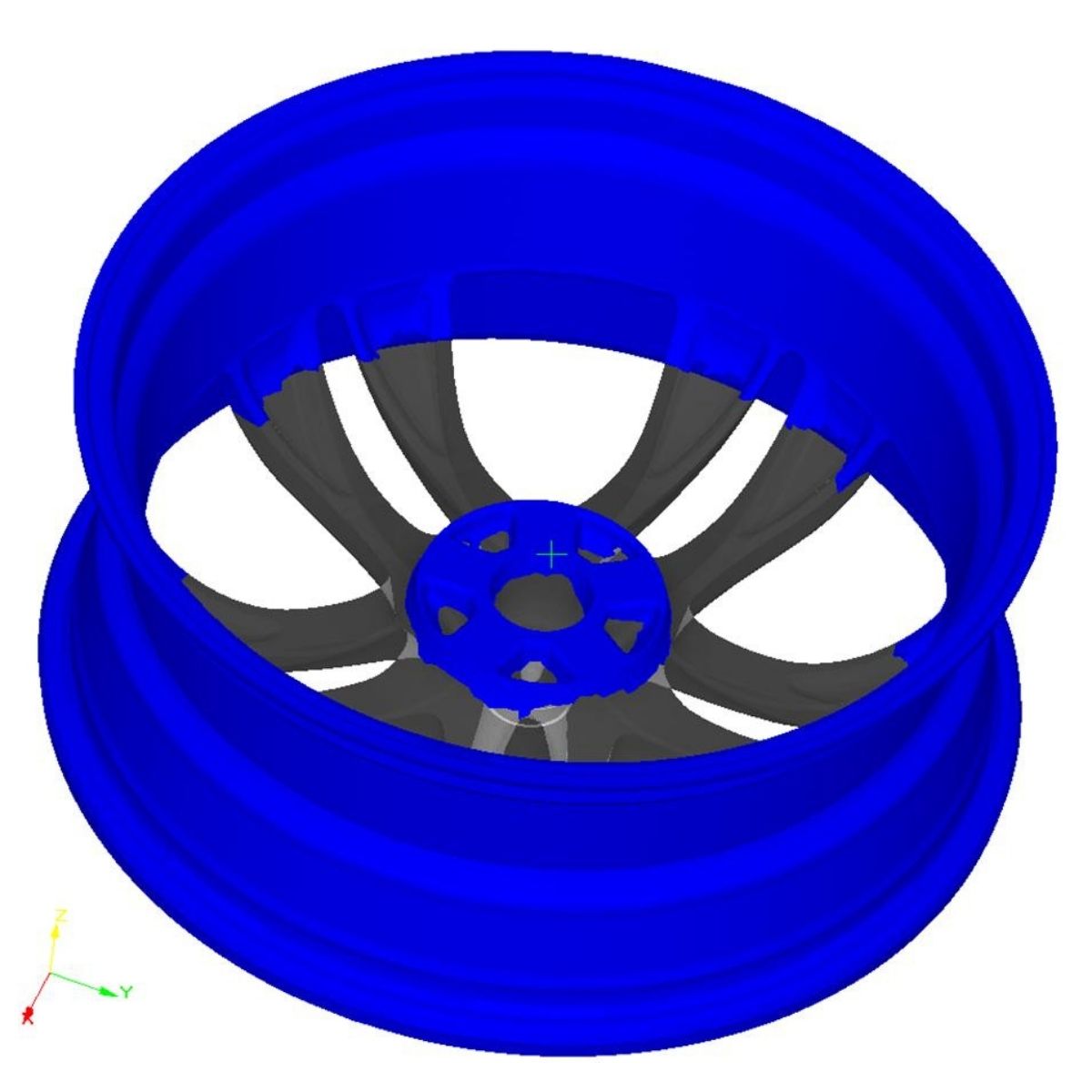
During filling there are two fluids in competition, the incoming alloy and the outgoing air.
The problem arises when the alloy is not able to completely fill the mould due to the resistance made by air.
During the low pressure casting process, the metal rises through a tube immersed in a molten metal bath with slight pressure applied on its surface. The features of the piece, which can even have very slim walls and fins, provide a finer and more compact grain casting, advantageous from the point of view of its mechanical features and its liquid and gas tightness.
Air and gas encapsulated by the alloy during filling cause porosity from gas and obstruct the stroke of the alloy, causing delamination and incompleteness. Vacuum solves the problem.
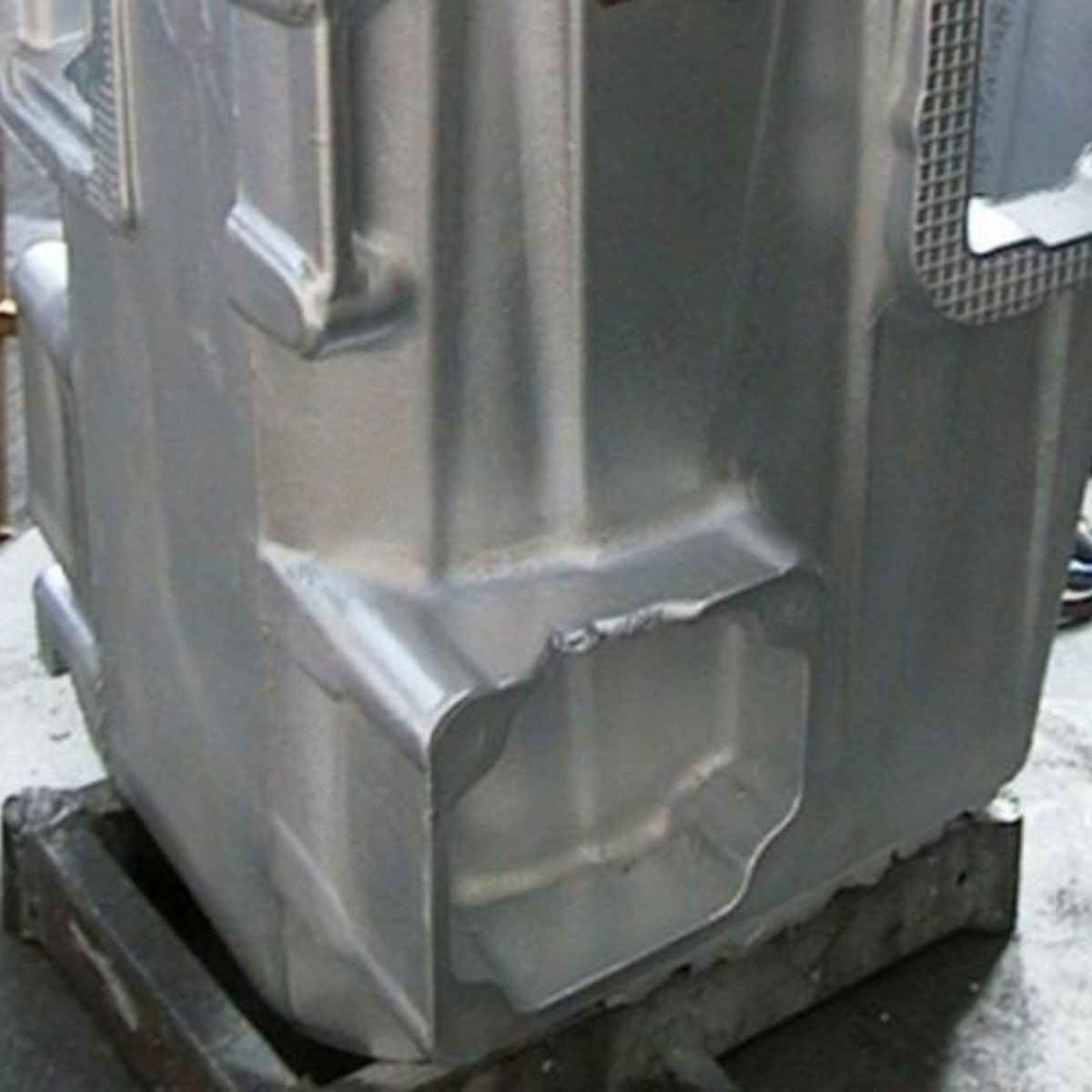
Vacuum low pressure provides the material with the specific mechanical features requested by the customer based on the final application, as it achieves a net reduction of gas porosity and of the micro porosity from shrinkage.
Elimination of air makes the piece more compact giving it better quality and mechanical strength. Furthermore, the net reduction of porosity and air inclusions make the piece more valid for subsequent mechanical and surface processes.
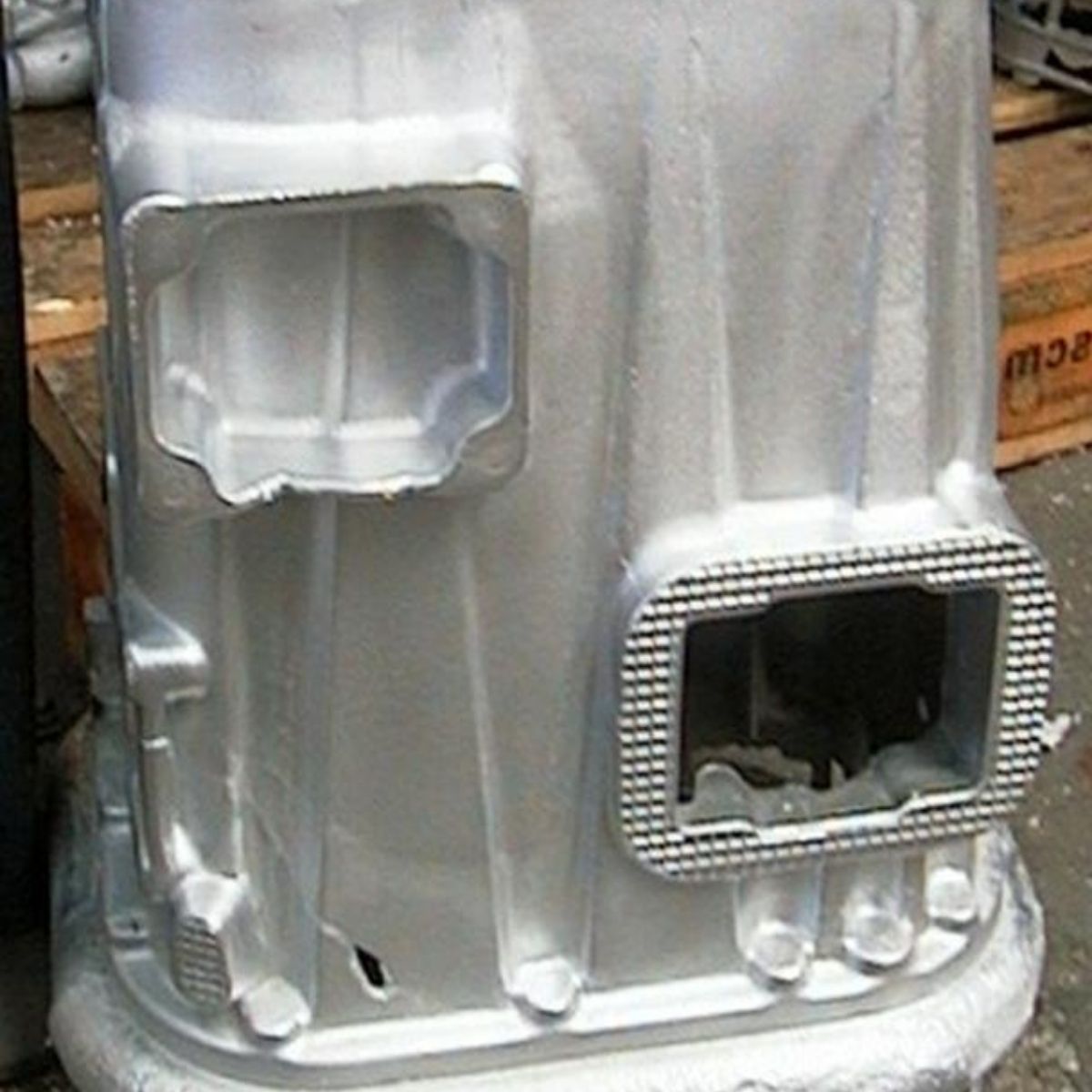
Vacuum is advantageous from the point of view of liquid and gas tightness and of the mechanical features as gas porosity and micro porosity from shrinkage are reduced, obtaining a well degassed and deoxidized product.
Vacuum low pressure can provide the material with the specific tightness requested by the customer based on the final application.
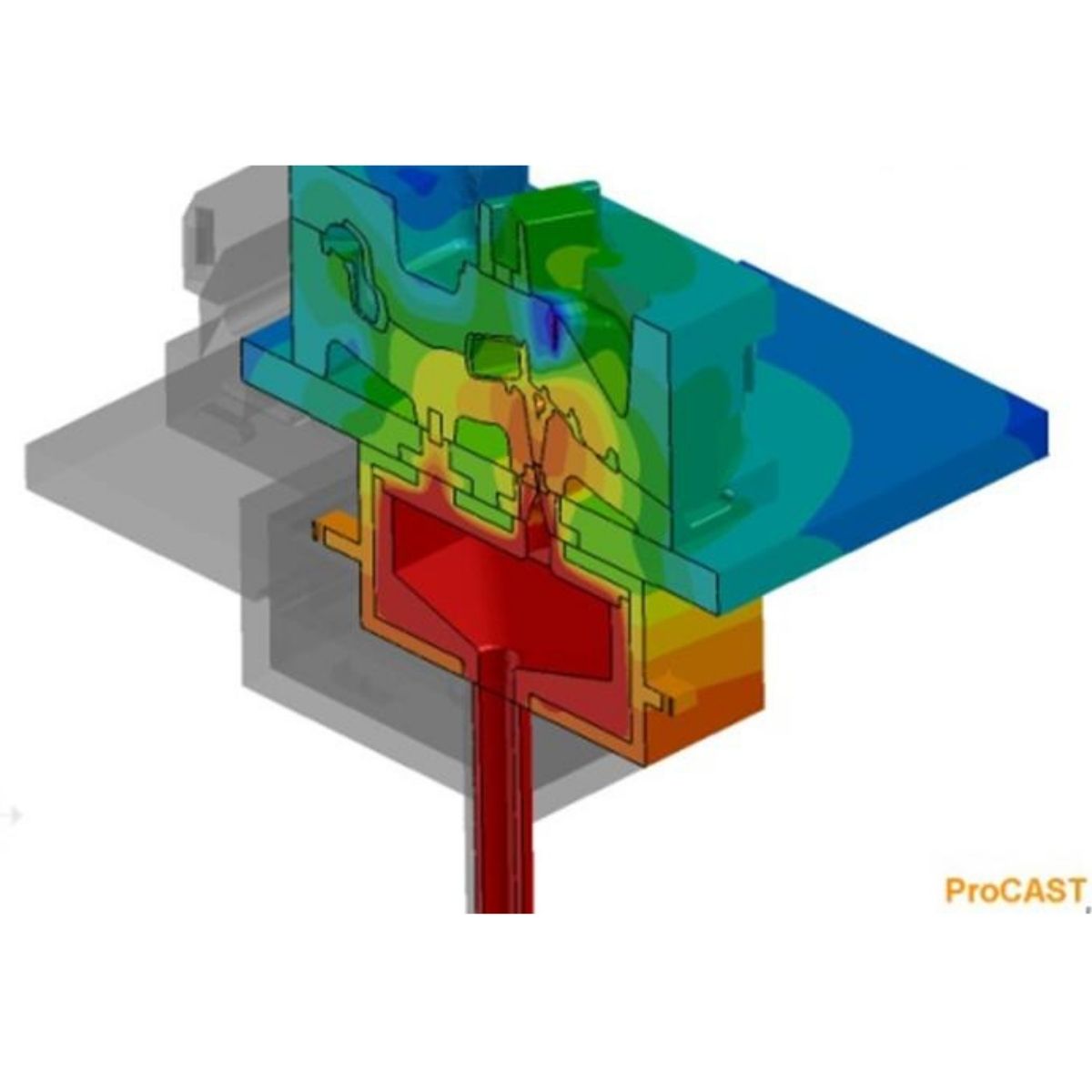
ECOTRE VALENTE, the indisputable specialist in vacuum application, studies the adaptation and optimal design of the mould, especially of the spout and vacuum channels:
– Determination of the evacuation system
– Adjustment of sizes and adaptation of the spout
– Adjustment of sizes and adaptation of the vacuum channels
– Consultancy on injection parameters
Contact us for information by filling out the form below.
Our technician-sales agent will get back to you.