The materials and the design of the die in a critical manufacturing step of an automotive shock absorber cap
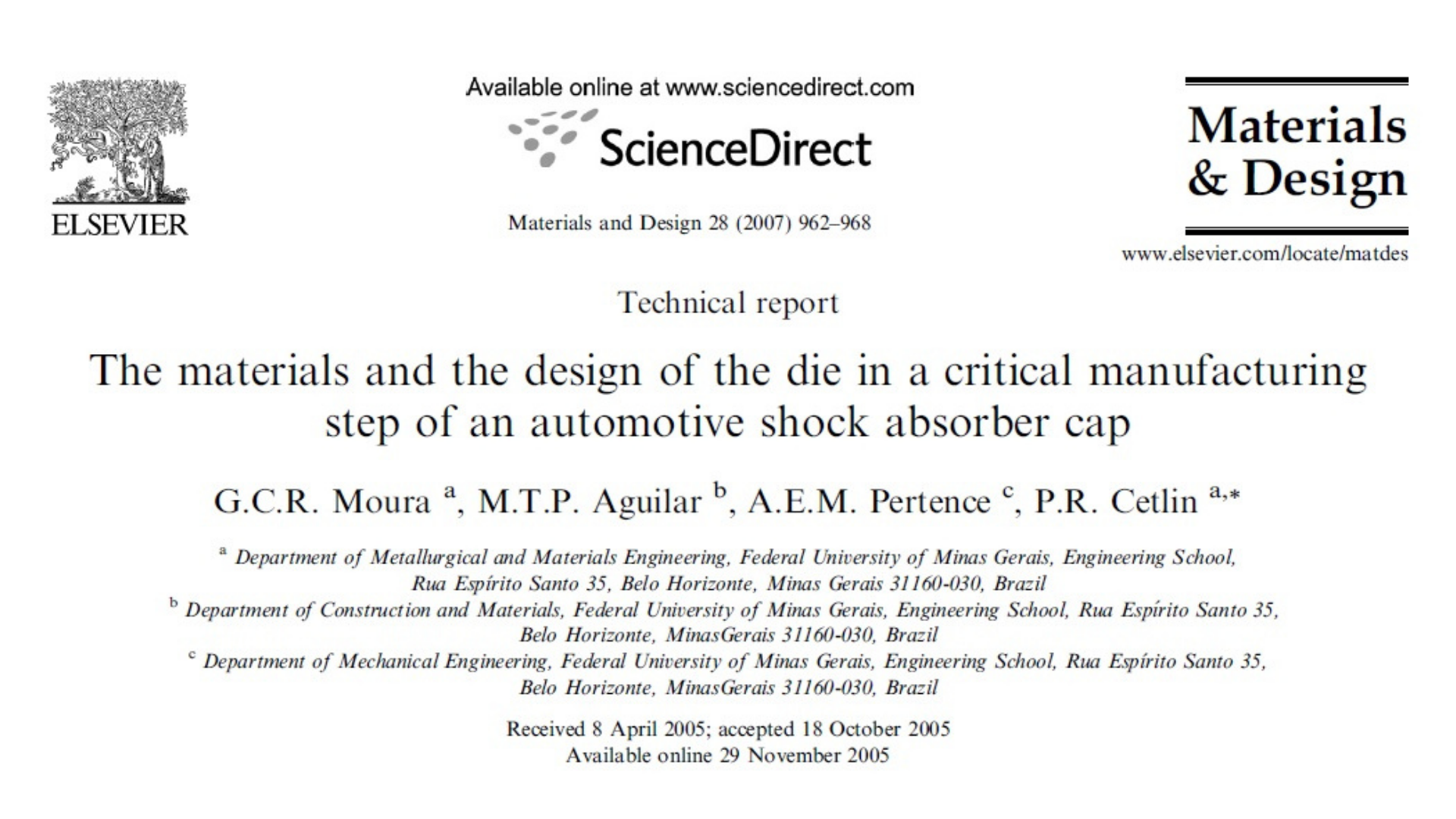
The materials and the design of the die in a critical manufacturing step of an automotive shock absorber cap
The industrial drawing of automotive shock absorber endcaps caused wear and radial brittle fractures of the tool steel dies. A finite element method (FEM) simulation of the process showed that this was caused by high contact and hoop stresses on the die. Such difficulties are usually solved by expensive changes in the die material, but a change in the punch design was proposed as a simpler and cheaper solution. The new punch geometries were employed in a FEM simulation of the drawing, indicating much lower contact and hoop stresses. The implementation of the solution eliminated the wear and brittle fracture problems.