QuikCAST and ProCAST Software Benefits
- Quality improvement
- Optimization and saving in the design
- Improvement of production
- Enhanced precision
- Flexibility of use
- Reduction of calculation times
- Reduction of production rejects
- Saves money
Core Blowing: What it is
The core blowing process is carried out using core blowing machines which, in a few instants, fill and compact the core casing through the injection of sand that blends with compressed air and binders. All the phases of the process are simulated: mould temperature control (for hot processes), blowing and gassing/curing.
Core Blowing Simulation: How it works
Blowing and gassing of cores in cold box, hot box and inorganic, Cordis, Inotec, Awb. Complete simulation of filling and of the thermal core casting.
The production of cores has traditionally always suffered from defects resulting from improper compacting of the sand, of low strength and poor surface finishes, resulting in a long and expensive development of trials and errors aimed at finding more appropriate process parameters. These typical basic defects are also responsible for the majority of the reject rates of the foundry sector. With the availability of numerical simulation solutions, the main process parameters can be optimized and reliable, allowing the effective cost and quality to be reached.
The core blowing module of the ProCAST simulation software predicts blowing and gassing defects, including incomplete filling, low compacting and little hardened areas; it is capable of predicting the behaviour of the sand and of the gas flow during the gassing stages when creating the core. ProCAST is a winning product that demonstrates that numerical simulation can be a convenient alternative to the long trial and error development procedures.
QuikCAST and ProCAST software has an innovative and easy-to-use graphical interface. It guides the user step-by-step in importing geometries, selecting materials and setting process parameters. These tasks require little effort by personnel. The following phase is calculation of the simulation, displaying how the piece is coming along while the software is computing. The standard 6, 8 and 12 core workstations are computers that reduce waiting times by a few hours for a complete simulation.
Results on hand, the core blowing simulation software automatically shows defects and problems that the core could produce in the department.
QuikCAST and ProCAST software is designed to operate on desktop PCs or workstations.
For the purchase, hire or a DEMO of the software or if you want to take advantage of a simulation service specially-made by our technical department, write or call us at +39 030 3365383
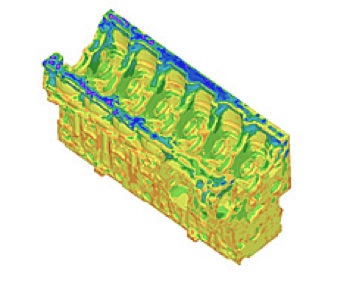
ELONGATION
The software can provide the elongation % map
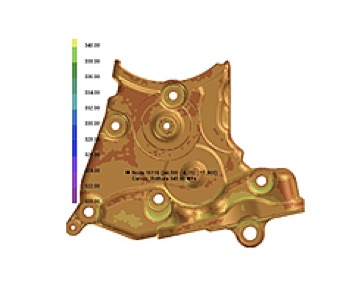
ULTIMATE TENSILE STRENGTH
The simulator provides the map of the Ultimate Tensile Strength of the Component “As Cast” and after Heat Treatment
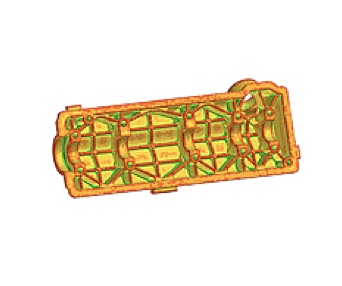
YIELD STRESS
The simulator provides the map of the Yield Stress of the Unfinished Component and after Heat Treatment
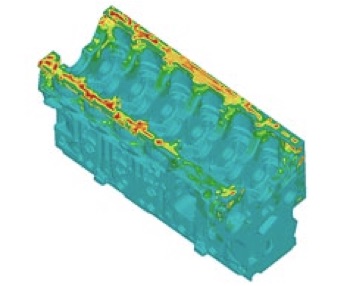
HARDNESS
The simulation can indicate the Hardness that can be obtained and its profile through its thickness
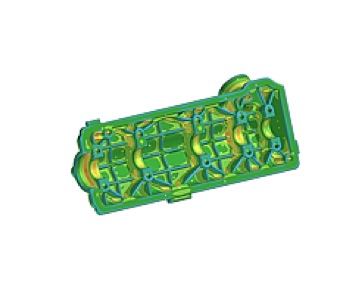
SDAS
The casting simulator shows the map of the SDAS (Secondary Dendrite Arm Spacing), a useful indicator of component performance
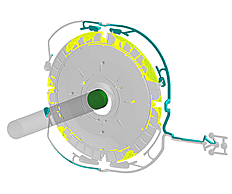
GAS POROSITY
Map of Porosity from Gas encapsulated during filling. Reduction of mechanical and bonding performance of the component
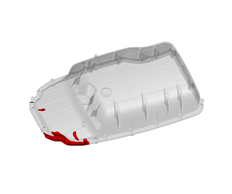
OXIDES
The alloy oxidizes during filling and the simulation points out where the oxides hide and where they move during filling
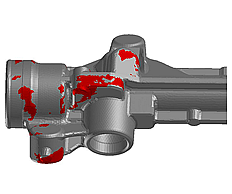
DELAMINATIONS
The simulator shows the delaminations, related to imperfect bonding of the alloy during filling
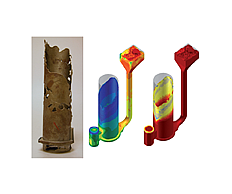
INCOMPLETENESS
Incomplete pieces or with joinings and retrieved lines
Undersized gating system or incorrect gas exhaust
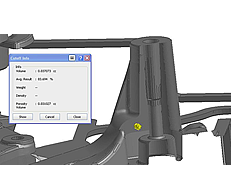
SHRINKAGE POROSITY
Map of Shrinkage Porosity.
Geography and Dimension of defect in mm3.
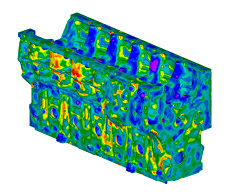
CRACKS
Map of hot and cold cracks on casting
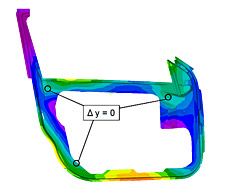
DIMENSIONAL
Dimensions and deformations of piece during solidification, extraction, cooling, blanking and any heat treatment
CO-DESIGN
Eliminate defects by acting on the causes and not on the effects
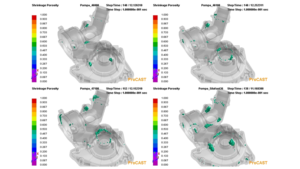
ALLOYS
Impact of the alloy on the mechanical features and on the defects
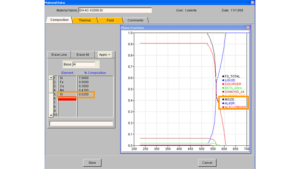
CHEMICAL ANALYSIS
QuikCAST Light, QuikCAST and ProCAST characterise the alloy initiating from the chemical analysis. Assessment, for example, of the consequences of the addition of 200 ppm of Strontium
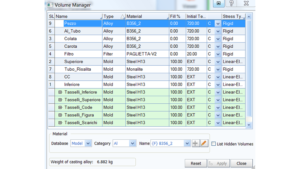
DATABASE
Complete archive of mould steels, sands, cores, insulation and exothermic sleeves, chillers, shells
DESCRIPTION
The simulation allows you to set a preview of the ideal process parameters for production of the component. This way the actual sampling underwent a positive result by eliminating fine tunings for the correct set of process parameters. Furthermore, the Optimizer Module of the software automatically defines the minimum and maximum ranges of the parameters guaranteeing the consistency and stability of the process.
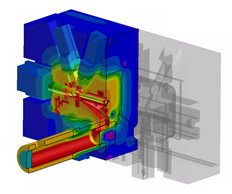
DIE
The casting simulation shows the thermal die cycling simulation, the conditioning or thermal circuits, lubrication, deformation and die duration
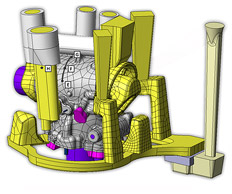
PLATE
Optimization of the plate, positioning of the chillers, sleeves, filters and die assembly of the cores. Maximum yield.
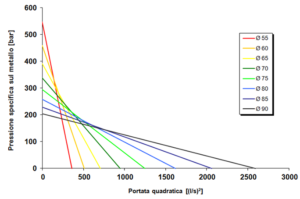
CASTING MACHINE
The casting simulation allows you to know the required casting machine and therefore the tonnes necessary
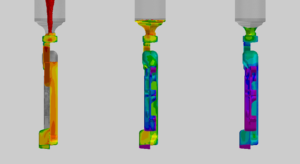
SYSTEM
Simulation of the entire injection cycle, complete with container, riser tube, tipping, automatic, manual system
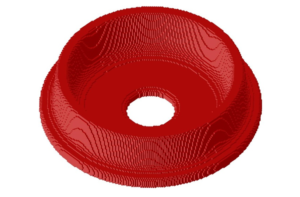
FINITE VOLUMES
The finite volumes or Finite Differences Technology is the introductory technology to casting simulation.
QuikCAST
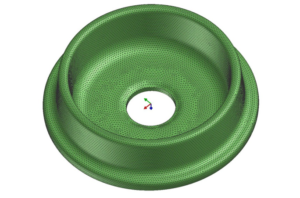
FINITE ELEMENTS
The Finite Elements Technology is the top technology that provides the maximum performance of the casting simulator.
ProCAST