QuikCAST and ProCAST Software Benefits
- Quality improvement
- Optimization and saving in the design
- Improvement of production
- Enhanced precision
- Flexibility of use
- Reduction of calculation times
- Reduction of production rejects
- Saves money
High Pressure Die Casting: What it is
Die casting is a process which entails introducing molten metal, held in a tank, into steel dies at a speed that allows for ideal filling time that guarantees the quality of the casting. The die, equipped with an articulated temperature control system, allows the casting to solidify quickly.
Once the form is sufficiently cool, the die opens and the resulting component can be removed. Die casting of metals can be carried out with hot chamber if the metal intended for casting is held inside a tank, in turn inside a furnace, or cold chamber if the metal tank is a cavity without temperature control.
HPDC Simulation: How it works
The entire injection cycle can be simulated with Cold Chamber, Hot Chamber machines and all alloys: Aluminum, Zama, Magnesium, Brass and Lead. Comprehensive simulation includes the presence of container, piston, dies, trolleys, plugs and blank holder. Thanks to the container, the QuikCAST e ProCAST software takes into account the total air and gas volume which obstructs filling and causes gas porosity, delamination and oxides. Thanks to the blank holder, the software computes the actual thermal condition of the die, which causes filling and solidification problems.
The die casting simulation matches reality if the software is capable of considering:
- the entire injection cycle, including pouring, waiting for injection consent, first and second phase
- the entire thermal die cycling simulation, including dies, trolleys, blank holder and thermal conditioning circuits
- gas and air in the cavity of the container and of the dies
- the actual effect of the third phase
The high pressure die casting simulation has always shown filling of the ‘die only’ starting from the sprue, disregarding pouring and injection in the container. This is due to the numerical limits of the casting simulation software incapable of integrally reproducing reality. In 2005 QuikCAST (Finite Differences) and ProCAST (Finite Elements) overcame this limit by switching to complete simulation. This made it possible to compare the results of the two simulations, with and without pouring and container. It turned out that the results of the simulation of the ‘die only’ can be misleading. On the other hand, the complete simulation of pouring and of the entire injection cycle was confirmed by the samplings.
AUDI AG FBT R8
Per gentile concessione di AUDI AG
https://www.audi mediacenter.com/en/photos/album/ audi r8 v10 performance rwd 1969 Bild Nr: A218768
https://www.audi mediacenter.com/en/search?query=Audi%20Space%20Frame&type=image Bild Nr: A192447
First of all, in the first, empirical calculations to determine the stroke at the start of phase II do not consider the geometry of the spouts, the tolerance of the loading systems (see sprue thickness variation) and therefore can provide incorrect information. Whereas, the complete simulation shows where the alloy is at a certain stroke, whether there are pre-chills, pre-spillages, turbulences and, therefore, it is possible to have simulated stroke-speed parameters compatible with reality. The injection curve simulated this way can be interfaced with the press.
In the second place, in the first the empirical and non-simulated evaluation of cooling of the alloy in the container can overestimate the temperatures with the appearance of defects in the castings such as cold joints. Whereas, the complete simulation shows the map of the alloy temperatures in the container and then, in a precise manner, the map during filling of the casting and therefore the critical zones are identified.
Thirdly, the simulation of the “die only” does not show the formation of waves and therefore encapsulation of gas which, then transported to the piece, determine gas porosity and oxide defects. Whereas the complete simulation shows the encapsulated air.
Fourthly, the data coming from sampling and production show that the same die, with the same piston, but mounted with containers of different lengths, require changing the process parameters to retain the metallurgic quality of the workpiece. This further information allows us to understand how simulation of the ‘die only’ is limited and inadequate.
In conclusion, the complete simulation of the die, container and pouring is essential to match reality.
Foundries that use die casting simulation software QuikCAST and ProCAST with the utmost satisfaction: Alupress, Faist, Far, Foma, Ghial, ZML,…
Die makers enthusiastic to virtualize the die casting process and to have a virtual press available: BGS, MCS, Stamec, Universal Stampi, …
Customers say about QuikCAST and ProCAST:
QuikCAST and ProCAST low pressure simulation software are accurate, fast and simple.
For the purchase, hire or a DEMO of the software or if you want to take advantage of a simulation service specially-made by our technical department, write or call us at +39 030 3365383
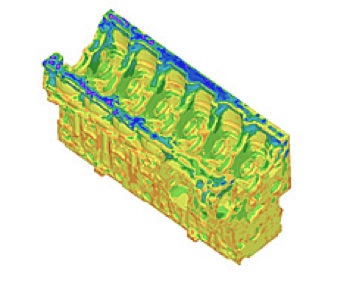
ELONGATION
The software can provide the elongation % map
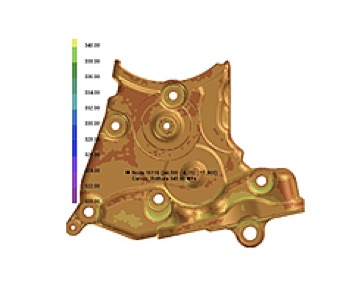
ULTIMATE TENSILE STRENGTH
The simulator provides the map of the Ultimate Tensile Strength of the Component “As Cast” and after Heat Treatment
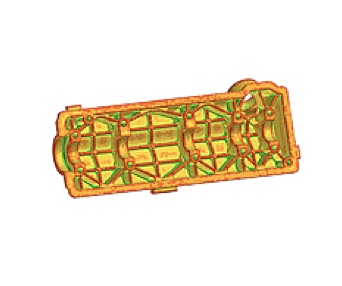
YIELD STRESS
The simulator provides the map of the Yield Stress of the Unfinished Component and after Heat Treatment
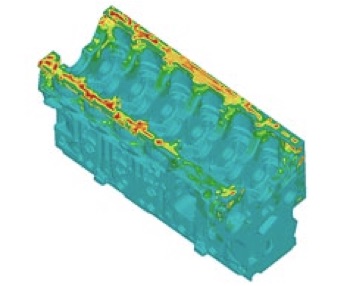
HARDNESS
The simulation can indicate the Hardness that can be obtained and its profile through its thickness
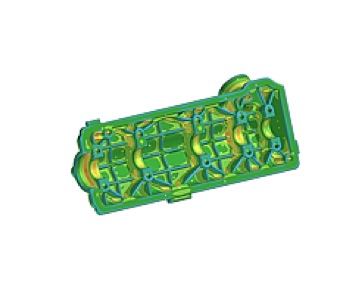
SDAS
The casting simulator shows the map of the SDAS (Secondary Dendrite Arm Spacing), a useful indicator of component performance
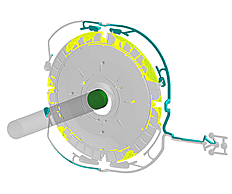
GAS POROSITY
Map of Porosity from Gas encapsulated during filling. Reduction of mechanical and bonding performance of the component
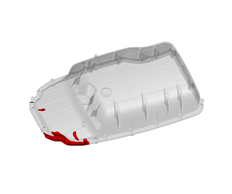
OXIDES
The alloy oxidizes during filling and the simulation points out where the oxides hide and where they move during filling
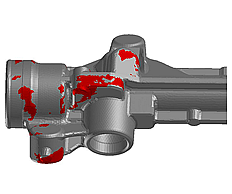
DELAMINATIONS
The simulator shows the delaminations, related to imperfect bonding of the alloy during filling
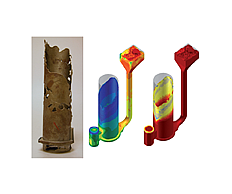
INCOMPLETENESS
Incomplete pieces or with joinings and retrieved lines
Undersized gating system or incorrect gas exhaust
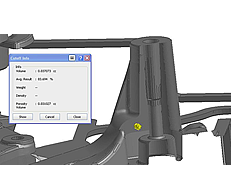
SHRINKAGE POROSITY
Map of Shrinkage Porosity.
Geography and Dimension of defect in mm3.
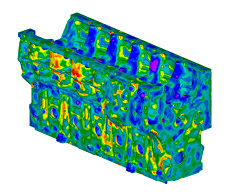
CRACKS
Map of hot and cold cracks on casting
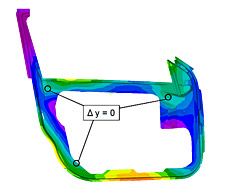
DIMENSIONAL
Dimensions and deformations of piece during solidification, extraction, cooling, blanking and any heat treatment
CO-DESIGN
Eliminate defects by acting on the causes and not on the effects
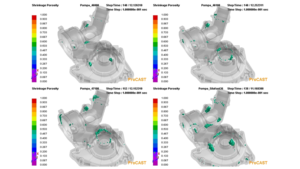
ALLOYS
Impact of the alloy on the mechanical features and on the defects
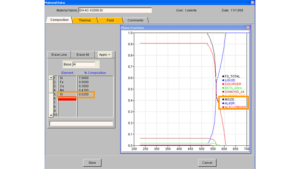
CHEMICAL ANALYSIS
QuikCAST Light, QuikCAST and ProCAST characterise the alloy initiating from the chemical analysis. Assessment, for example, of the consequences of the addition of 200 ppm of Strontium
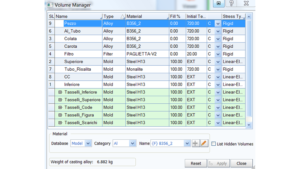
DATABASE
Complete archive of mould steels, sands, cores, insulation and exothermic sleeves, chillers, shells
DESCRIPTION
The simulation allows you to set a preview of the ideal process parameters for production of the component. This way the actual sampling underwent a positive result by eliminating fine tunings for the correct set of process parameters. Furthermore, the Optimizer Module of the software automatically defines the minimum and maximum ranges of the parameters guaranteeing the consistency and stability of the process.
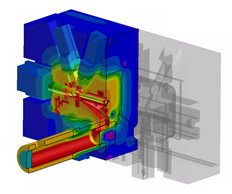
DIE
The casting simulation shows the thermal die cycling simulation, the conditioning or thermal circuits, lubrication, deformation and die duration
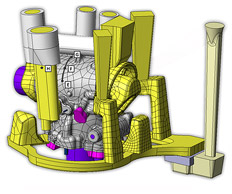
PLATE
Optimization of the plate, positioning of the chillers, sleeves, filters and die assembly of the cores. Maximum yield.
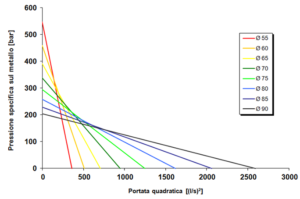
CASTING MACHINE
The casting simulation allows you to know the required casting machine and therefore the tonnes necessary
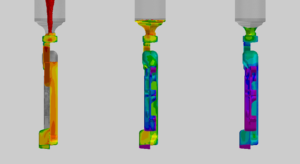
SYSTEM
Simulation of the entire injection cycle, complete with container, riser tube, tipping, automatic, manual system
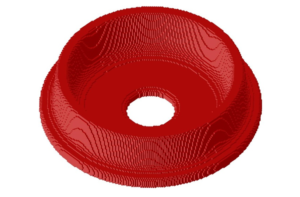
FINITE VOLUMES
The finite volumes or Finite Differences Technology is the introductory technology to casting simulation.
QuikCAST and QuikCAST Light
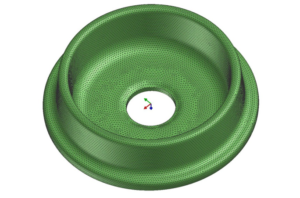
FINITE ELEMENTS
The Finite Elements Technology is the top technology that provides the maximum performance of the casting simulator.
ProCAST